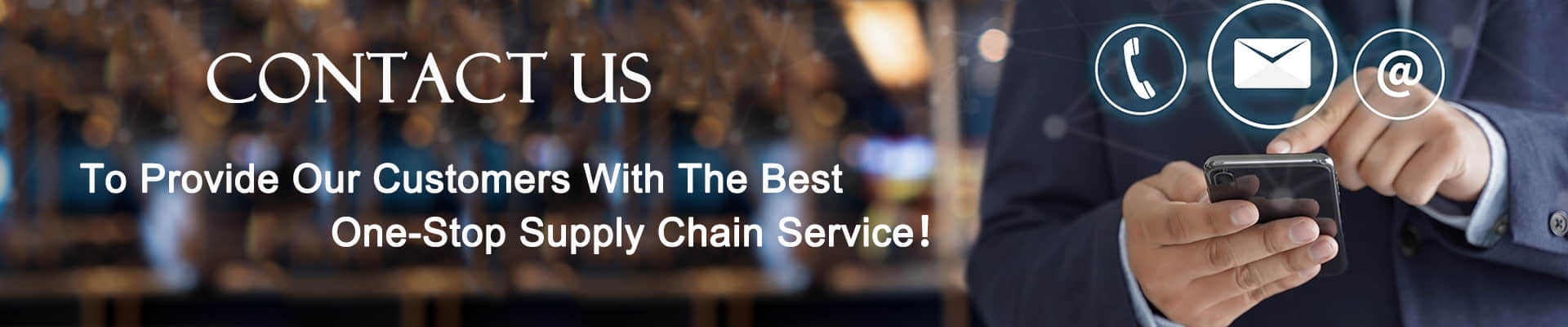
Disc-type scaffolding product manual
A.Product Introduction
Disc scaffolding is a new type of scaffolding, which was introduced from Europe in 1980s, and is an upgraded product after the bowl buckle scaffolding. It is also called daisy disc scaffolding system, insert disc scaffolding system, wheel disc scaffolding system, buckle disc olding system, and rayon scaffolding, etc. The scaffold socket is a disc with 8 holes, 4 large and 4 small.
The crossbars are inserted at 90°perpendicular to the derivative frame into the small holes and the diagonal bars into the large holes. The cross bar can also be inserted into the large hole, and the angle can be adjusted within 15°. Widely used in: general viaduct and other bridge projects, tunnel projects, factory buildings, elevated water towers, power plants, oil refineries, etc. And special plant support design, also suitable for street bridges, span scaffolding, storage shelves, chimneys, water towers and indoor and outdoor decoration, large concert stage, background frame, stands, viewing stands, modeling frame, staircase system, sports competition stands and other projects.
B. Product composition
It is mainly composed of uprights,
horizontal rods, vertical inclined rods, horizontal inclined rods, adjustable
bases and adjustable top brackets, etc.
1 - riser; 2 - riser connecting tube; 3 -
riser connector; 4 - connecting plate; 5 - pin; 6 - crossbar. 7-Vertical
inclined rod; 8-Horizontal inclined rod; 9-Adjustable base; 10-Adjustable top
bracket
C. assembly method
Bite the crossbar plug into the disc of the
upright, then insert the locking pin into the small hole of the disc and secure
it with a hammer. To connec t the
uprights, simply place one upright over the inner sleeve of the other upright.
After installing the crossbar and upright, the locking pin of the tilt rod can
be inserted into the large hole of the disc, making the crossbar and upright
form a triangular structure to fix the whole system.
D. the system set up requirements
1.For interior wall support.
1). When the disc support system is erected
formwork bracket, the erection height ≤ 24m; when it is greater than 24m, it should
be designed and calculated separately.
2). When the disc support system is set up
as formwork support, the size of the column should be calculated according to
the construction plan and the horizontal rod of fixed length column, adjustable top bracket and
adjustable base should be inserted according to the combination of support
height.
3). When erecting the full hall formwork
bracket of height ≤ 8m, the step distance ≤ 1.5m.
4). When erecting full hall formwork
bracket with height ≥ 8m, the vertical diagonal bar should be set in full, the
step distance of the horizontal bar ≤ 1.5m, and the horizontal layer diagonal
bar should be set every 4-6 sections along the height, and should be reliably
tied with the surrounding structure trip. For long independent high support mold
frame, the ratio of the total height of the frame and the width of the frame H/B
should not be more than 3.
5). The cantilever length of the adjustable
top bracket of the formwork bracket upright rod extending the top horizontal
rod ≤ 650mm, and the adjustable base inserted into the upright rod length ≥150mm
(below); the horizontal rod step distance of the topmost layer of the shelf
should be reduced by one disk buckle spacing than the standard step.
2.For exterior walls.
1). When using disc scaffolding to erect
double-row external scaffolding, the height ≤ 24m, > 24m, must be
additionally designed and calculated. Users can choose the geometric size of
the scaffold according to the requirements of use, and the step distance of the
cross bar of the phase collar should be 2m, the vertical distance of the
vertical bar should be 1.5m or 1.8m, and should not be greater than 2.1m, and
the cross distance of the vertical bar should be 0.9m or 1.2m.
2). Diagonal rod or scissor brace: one
vertical diagonal rod should be set for every 5 spans per floor along the
outside of the frame longitudinally.
3). Connecting wall members must be used to
withstand the tensile and compressive loads of rigid rods, connecting wall
members set two steps three spans.
4). Each step of the horizontal bar layer
of double-row scaffolding, when there is no hooked tread or other hooked
scaffold plate to strengthen the rigidity of the horizontal layer, should be
every 5 span set horizontal inclined rod.
E. Packaging requirements
All types of products should be packaged
according to the name and specifications of the classification bundle. Each
package should be marked with the product name, specifications, quantity and
other content of the label.
F. Transportation requirements
Do not mix with corrosive substances for
transportation.
During transportation and loading and
unloading, squeezing and throwing are strictly prohibited to prevent product
deformation and damage.
G. Storage requirements
Products should be stored according to name
specifications.
The product should be placed in a dry place to prevent media erosion and rain, snow, water immersion damage.
Categories
New Blog
Copyright © 2025 AJ CENTURY GROUP. All Rights Reserved.
IPv6 network supported
Friendly Links :
AJ Scaffolding